in the last reaction I was pointed by Rudi to the fact that TPI does not automatically imply a division in smaller parts when curvature gets bigger. triangular tesselation also works for dividing a surface into planes.
the reason for making a smaller division when curvature is larger is mainly for making the elements (with a certain thickness) more plane-like and easier to produce. My assumption was that when a surface gets larger curvature it needs to have a finer division in order to make the elements easier to produce. It would make the components less wedge shaped.
In fact, the divide-option in Grasshopper seems to generate a bigger division at the less curved borders of the surface (figure 2), maybe a variable divsion depending on curvature is not a necessity.
Paul de Ruiter (TOI) advised me to look carefully at the connections/joints between the components. The connections are influencing both the structural and physical performance of the facade. Also he mentioned spray-composites as a possible finish. fibre reinforced resin that can be applied by spraying (and maybe by dipping as well)
the connections are limited by:
- the geometry that can be created by a milling machine (figure 5)
- the surface finishing of the elements (possibility for adding seals for instance)
- the stuctural connection
The aim is to keep the structural connection really flexible, so it works for every variable element configuration (As seen in the protospace pavilion by ONL, connections between the frame and cladding always fit). maybe flexible strips can offer a solution.
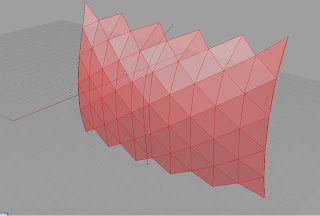
figure 1
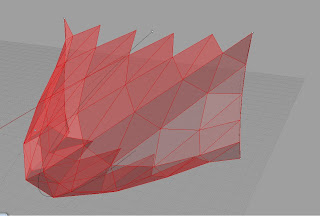
figure 2
the coarse division could also have elements whit a curved outer surface in order to make it approximate the master surface.
possible disadvantage - elements become wedge shaped, difficult milling? (only in a 2,5-axis machine, or with complex edge detail)
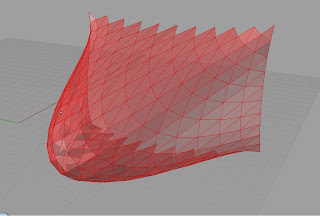
figure 3
a smaller division decreases the difficulties caused by wedge-shape, but more elements are needed, which possibly has negative effect on strength, watertightness and reduces the possibility to add windows to the structure
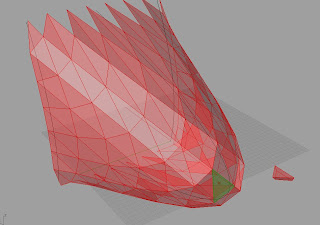
figure 4
extracted element from a free formed main surface
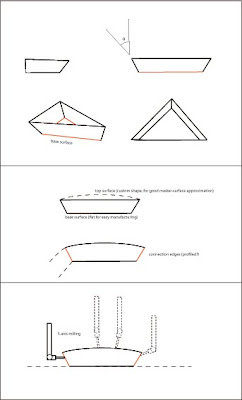
figure 5